The Ultimate Guide to Forklift Maintenance: Ensuring Safety and Efficiency
Key Takeaways
Takeaway | Description |
---|---|
Preventive Maintenance | Regular check-ups prevent major issues and prolong forklift life. |
Certified Technicians | Utilizing skilled technicians for repairs ensures safety and efficiency. |
Custom Maintenance Plan | Tailoring a plan to specific forklift types and usage can significantly reduce downtime. |
Safety Compliance | Adhering to safety standards is crucial for operational efficiency and worker safety. |
Cost Savings | Regular maintenance can lead to significant long-term savings by avoiding major repairs. |

Understanding Forklift Maintenance
Forklifts are vital tools in numerous industries, playing a crucial role in material handling and logistics. Regular maintenance is not merely a regulatory requirement; it’s the foundation of operational safety and efficiency. This section explores the significance and methodology of routine forklift maintenance.
The Importance of Regular Maintenance
Why it matters: Regular maintenance ensures that forklifts are operating at peak efficiency and safety. It helps identify potential issues before they escalate into costly or hazardous situations. Consistent check-ups and services can extend the lifespan of the machinery, prevent accidents, and save money on emergency repairs.
Crafting a Maintenance Schedule
A structured forklift maintenance schedule is vital for the longevity and reliability of your forklift fleet. This section guides you through creating a routine that aligns with your operational needs and industry standards.
Periodic Maintenance Checklists
Stay organized: A checklist for daily, weekly, and monthly forklift maintenance tasks ensures that all crucial checks are performed regularly. This includes checking fluid levels, inspecting brakes and tires, and ensuring that all safety features are functional.
Monthly Forklift Maintenance Schedule (Every 200 to 250 operating hours):
Task | Description |
---|---|
Oil change | Change the engine oil to ensure smooth operation and engine longevity. |
Air filter service | Clean or replace the air filter to improve performance and fuel efficiency. |
Hydraulic lines inspection | Check hydraulic lines for cracks and replace as needed to ensure safety and prevent leaks. |
Clean the battery | Clean the top of the forklift battery with battery cleaner or warm water. |
Battery pH check | Ensure the battery pH is between 5 and 7. |
Lift chain tension | Check and adjust the tension of the lift chain as needed. |
Hydraulic oil pump check | Inspect the hydraulic oil pump for proper operation and signs of wear. |
Chassis links and bushing adjustments | Adjust the chassis links, mast support bushing, and tilt cylinder pins. |
Annual Forklift Maintenance Schedule (Every year or 2,000 hours):
Task | Description |
---|---|
Fluid replacements | Replace the brake fluid, engine coolant, fuel filter, and fuel strainer element. |
Mast welds and forks test | Perform magnetic particle testing on the main mast welds and forks. |
Hoses and fittings test | Test all hoses, couplings, fittings, and connections to the cylinders in the main mast assembly and the tilt control system. |
Lifting capacity inspection | Ensure the forklift can lift the maximum load specified by the manufacturer. |
Hydraulic lines inspection | Annually inspect and replace hydraulic lines as needed. |
The Role of Certified Technicians
Understanding their Importance: Forklift maintenance technicians are vital for ensuring that these machines operate safely and efficiently in the workplace. They play a crucial role in maintaining and repairing forklifts, including regular inspections to identify any faults or potential hazards, such as checking brakes, steering mechanisms, and hydraulic systems. Their deep understanding of mechanics and electrical systems, especially for modern forklifts operating on batteries or hybrid power sources, is essential. They are not only responsible for maintaining the forklifts but also for training employees on proper operation techniques, thereby preventing accidents due to operator error.
Qualifications and Training: Proper training and certification are crucial for forklift technicians. They must complete specialized training programs that cover safety procedures, forklift maintenance practices, troubleshooting techniques, and more. Additional certifications from industry bodies like the National Institute for Automotive Service Excellence (ASE) or the Forklift Training Institute (FTI) might be required. This extensive training and certification ensure that technicians can maintain forklifts safely and efficiently, identifying potential issues before they become problems and performing regular maintenance tasks to keep machinery functioning optimally.
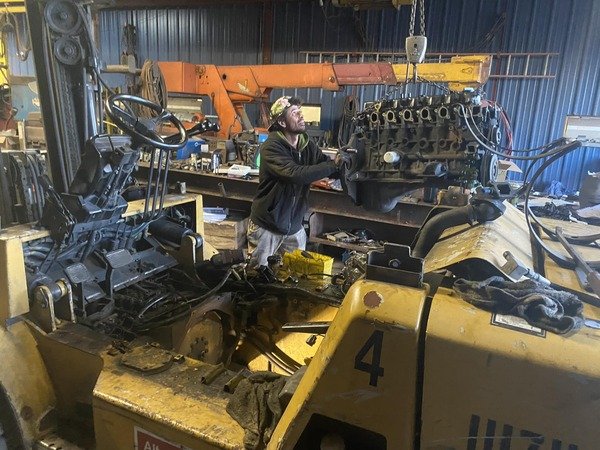
Finding the Right Service Provider
Factors to Consider: Choosing a dependable forklift service provider is an indispensable business decision. It’s essential to look for providers that offer comprehensive maintenance plans, which are more cost-effective in the long run and ensure regular maintenance. Research the provider’s reputation thoroughly, including references, customer testimonials, and the expertise of their technical staff. Evaluate the quality of customer support, including their responsiveness to urgent needs or breakdowns. Finally, assess their pricing model to ensure it offers value for money, balancing cost-effectiveness with quality service.
Benefits of a Maintenance Plan: Investing in a maintenance plan offers peace of mind, assuring that the service provider will perform regular maintenance on your forklifts in a timely manner. These plans anticipate and address issues early on, significantly reducing the risk of unexpected breakdowns and the possibility of staff injury caused by faulty equipment. In the long term, maintenance plans are more economical, as they prevent serious damage to your forklifts and save on costs that would arise from separate maintenance tasks.
Maintenance Best Practices
Regular Inspections and Immediate Attention: Regular inspections are a cornerstone of forklift maintenance, helping to identify and address issues immediately. This includes checking controls, fluid levels, drive systems, tires, and safety systems among others. Early detection of problems can prevent costly repairs in the future, ensuring that forklifts remain operable for longer periods. The frequency and quality of maintenance are directly proportional to safety, significantly reducing the risk of equipment breakdowns and worker injuries.
Comprehensive Maintenance Plans: Maintenance plans are crucial for consistent care. They provide a structured approach to forklift maintenance, covering all routine needs at set intervals. This organized approach is not only cost-effective but also ensures that no aspect of the forklift’s maintenance is overlooked. It’s a proactive measure that maintains the forklift’s operational efficiency, safety, and longevity, ultimately contributing to the smooth running of operations.
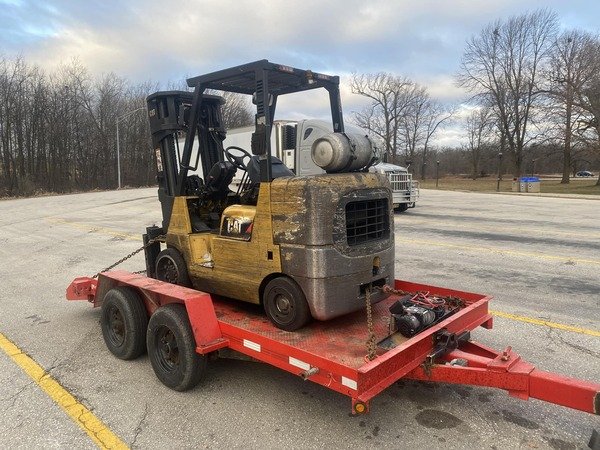
Preventive Measures
Proactive care: Regular preventive maintenance is crucial for forklift operation. Planning maintenance activities reduces costs, minimizes unexpected downtime, and avoids fines associated with non-compliance to safety standards like OSHA. A well-maintained forklift ensures years of reliable service, increases productivity by preventing unexpected breakdowns, retains higher residual value, and most importantly, enhances safety by reducing the risk of accidents due to equipment failure.
Creating a Preventive Maintenance Plan: A consistent plan should include daily inspections by operators for fluid levels, visible damage, tire condition, forklift cleanliness, and the functionality of safety devices. This routine vigilance helps in spotting minor issues before they escalate into major problems, ensuring the forklift operates safely and efficiently.
Record Keeping and Documentation
Track progress: Maintaining detailed records of all maintenance activities is not only a best practice but also a regulatory requirement. OSHA sets specific guidelines for occupational health and safety, including forklift maintenance. Proper documentation supports effective maintenance planning, helps in warranty claims, and ensures legal compliance. It provides a clear history of the forklift’s condition and maintenance, which is invaluable for troubleshooting issues, scheduling future service, and even determining the forklift’s resale value.
Safety First: Compliance and Training
The critical role of safety standards and training: Compliance with OSHA regulations is non-negotiable. Ensuring that all maintenance staff are adequately trained and aware of the latest safety regulations is essential for a safe working environment. Training should cover the proper use and inspection of forklifts, understanding of maintenance schedules, and awareness of the common signs of wear and tear. A well-trained team can effectively identify and address issues early, contributing significantly to the overall safety and longevity of the forklift.
Understanding OSHA Regulations
Overview of OSHA’s Role: The Occupational Safety and Health Administration (OSHA) sets and enforces regulatory standards to keep workers safe, with forklift safety being one of the most crucial aspects across various industries. OSHA’s Powered Industrial Truck regulations, which cover a broad range of safety topics, are designed to ensure that forklifts are ready and able to perform jobs safely. Proactive and responsible adherence to these regulations leads to fewer accidents, lost time incidents, and safer workplaces overall. Specific attention is given to electromechanical maintenance, pre-operation checkout, operational testing, and the facilities involved in preparing the forklift to do its job. Compliance with these standards is essential for both safety and avoiding costly fines.
Electric Lifts & Batteries and IC Lifts: OSHA also sets specific guidelines for electric lifts and batteries, requiring understanding and active management of battery-related hazards. This includes provisions for safe handling, storage, and the necessary equipment for battery-changing operations. For internal combustion (IC) lifts, OSHA’s standards cover fuel handling, ventilating toxic fumes, and ensuring proper refueling practices. Both types of lifts require diligent daily and operational inspections to identify and report any unsafe conditions, ensuring no forklift is operated when tagged for maintenance.
Addressing Downtime and Emergency Repairs
Preventive Maintenance: Regular inspection, cleaning, and maintenance of forklifts, along with the replacement of worn-out or broken parts, are key strategies for reducing downtime. By detecting potential problems early, you can prevent extended periods of inactivity and ensure forklifts remain in good working condition. Regular servicing according to manufacturer guidelines is crucial, as is addressing any repairs promptly.
Operator Training and Technology Use: Adequately training operators is vital to minimize downtime. Properly trained operators are less likely to cause breakdowns and can identify potential issues early. Utilizing technology to monitor and track forklift performance can also help identify problems before they lead to breakdowns. Automating maintenance scheduling and repair tasks can further reduce downtime, improving overall efficiency and reducing the chances of unexpected breakdowns.
Creating a Backup Plan
Understanding the Impact of Downtime: Any disruption in daily workflow, especially in a warehouse environment where forklifts facilitate heavy lifting, can have a significant financial impact. Regular maintenance and service of machinery are critical to preventing such disruptions. The age of your forklift fleet, the number of forklifts, the complexity of the units, and the operating environment all play a part in determining a good maintenance schedule and the need for backup plans.
Fleet Size and Alternating Units: Companies with larger fleets typically have backups in the event of a breakdown, allowing them to alternate units and reduce wear on any single forklift. Smaller fleets or warehouses with only a few forklifts face greater risks if a unit breaks down. Regular maintenance and having a plan for quick replacements or rentals can greatly reduce the risk of operational interruptions. Seasonal businesses, in particular, should aim to service their forklifts before peak seasons and have contingencies in place for any unexpected downtime.
By understanding and adhering to OSHA regulations, implementing proactive strategies for maintenance and repairs, and having a solid backup plan, you can ensure the safety, efficiency, and continuous operation of your forklift fleet.
Conclusion: The Value of Forklift Maintenance
Summarizing the key benefits of a well-executed maintenance plan, including enhanced safety, reduced operational costs, and improved equipment lifespan. Regular maintenance is not just about compliance; it’s a strategic approach to ensuring the safety of your operators and the efficiency of your operations.
With the right approach and commitment to regular upkeep, your forklifts can serve as reliable, safe, and efficient components of your business for years to come. Remember, a small investment in regular maintenance can prevent costly downtime and accidents, contributing significantly to the overall success and safety of your operations. If you’d like to learn more about forklifts please visit our blog.